Plastic extrusion for tubing, profiles, and custom shapes
Plastic extrusion for tubing, profiles, and custom shapes
Blog Article
Checking Out the Different Strategies and Technologies Behind Plastic Extrusion
The realm of plastic extrusion is a mix of technology, accuracy, and modern technology, pivotal to countless sectors worldwide. Advanced machinery, electronic controls, and a variety of products converge in this complex procedure, creating high-quality, sturdy products.
Recognizing the Basics of Plastic Extrusion
The procedure of plastic extrusion, usually hailed as a keystone in the world of manufacturing, forms the bedrock of this conversation. In significance, plastic extrusion is a high-volume production procedure in which raw plastic material is thawed and formed right into a continuous profile. The procedure begins with feeding plastic products, usually in the type of pellets, right into a heated barrel.
The Duty of Different Products in Plastic Extrusion
While plastic extrusion is a frequently used strategy in production, the materials utilized in this process greatly influence its final outcome. Various kinds of plastics, such as polyethylene, PVC, and Abdominal, each offer one-of-a-kind buildings to the end item. Producers should carefully take into consideration the residential properties of the product to maximize the extrusion process.
Techniques Utilized in the Plastic Extrusion Process
The plastic extrusion process entails different strategies that are vital to its procedure and effectiveness (plastic extrusion). The conversation will begin with a simplified description of the essentials of plastic extrusion. This will be complied with by a failure of the procedure in information and an exploration of approaches to improve the efficiency of the extrusion strategy

Understanding Plastic Extrusion Basics
In the realm of production, plastic extrusion stands as an essential process, crucial in the production of a multitude of day-to-day products. At its core, plastic extrusion entails changing raw plastic product right into a continuous profiled form. This is accomplished by melting the plastic, usually in the type of pellets or granules, and requiring it through a designed die. The resulting product is a lengthy plastic item, such as a cable, panel, or pipeline covering, that keeps the form of the die. This cost-efficient method is highly functional, able to produce complicated forms and accommodate a variety of plastic products. Basic understanding of these fundamentals permits more exploration of the more elaborate elements of plastic extrusion.
Comprehensive Extrusion Refine Breakdown

Improving Extrusion Method Efficiency
Performance gains in the plastic extrusion procedure can considerably affect both the high quality of the end product and the overall performance of the procedure. Continual optimization of the extrusion strategy is important to keeping a competitive side. Methods that improve efficiency typically entail exact control of temperature and pressure throughout the process. Modern technologies, such as computerized systems and sensors, have been crucial in attaining this control. The use of high-quality raw materials can reduce waste and improve output quality. Normal maintenance of extrusion devices can also reduce downtimes, therefore raising efficiency. Lastly, embracing lean production concepts can assist remove unnecessary actions in the process, promoting efficiency gains.
Just How Technology Is Changing the Face of Plastic Extrusion
The advent of new modern technology has actually considerably changed the landscape of plastic extrusion. It has resulted in the advancement of innovative extrusion machinery, which has boosted the effectiveness and high quality of the plastic extrusion procedure. Innovations in the extrusion procedure have also been driven by technological innovations, using improved abilities and convenience.
Advanced Extrusion Machinery
Revolutionizing the realm of plastic extrusion, advanced equipment imbued with innovative modern technology is ushering in a new period of effectiveness and precision. These devices, geared up with innovative attributes like self-regulating temperature control systems, make certain ideal problems for plastic handling, consequently lessening waste and improving product top quality. While these improvements are already impressive, the continual development of technology guarantees also greater jumps forward in the field of plastic extrusion machinery.
Advancements in Extrusion Processes
Using the power of modern technology, plastic extrusion processes are undertaking a transformative metamorphosis. With the development of 3D printing, the plastic extrusion landscape is also broadening into brand-new realms of opportunity. These technological developments are not just enhancing the top quality of extruded plastic products yet likewise pushing the industry towards an extra lasting, reliable, and innovative future.
Real-World Applications of Plastic Extrusion
Plastic extrusion, a effective and functional procedure, explanation finds use in countless real-world applications. It's predominantly utilized in the manufacturing sector, where it's utilized to produce a myriad of products such as pipes, tubings, window structures, weather stripping, and fencing. The automotive market likewise uses this innovation to generate parts like plastic and trim sheet. The clinical field counts on extrusion for the manufacture of catheters, IV tubes, and other medical devices. Also in food manufacturing, extrusion contributes in creating products like pasta or grain. The toughness and flexibility of plastic extrusion, paired with its cost-effectiveness, make it an indispensable procedure across different industries, underscoring its prevalent sensible applications.
The Future of Plastic Extrusion: Forecasts and Patterns
As we aim to the perspective, it becomes clear that plastic extrusion is poised for significant improvements and makeover. New technologies guarantee to revolutionize the sector, from intelligent equipment that makes best use of effectiveness to sustainable products that reduce environmental impact. Automation and robotics are forecasted to play a larger duty, enhancing production and guaranteeing consistent top quality. Environment-friendly choices to conventional plastic, such as bioplastics, are likewise expected to get grip. These materials not only assist to save resources yet additionally decrease waste, lining up with international sustainability objectives. On the other hand, improvements in 3D printing are predicted to open up brand-new possibilities for customization. These patterns indicate a vibrant, developing future for plastic extrusion, driven by technological technology and a commitment to sustainability.
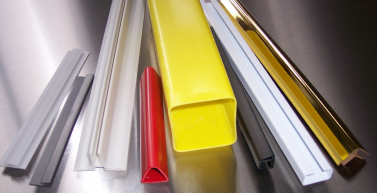
Conclusion
In final thought, plastic extrusion is an intricate process that utilizes innovative modern technology and differed products to develop diverse products. As plastic manufacturing continues to develop, it visit homepage remains a crucial part of many industries worldwide.
In significance, plastic extrusion is a high-volume manufacturing anonymous process in which raw plastic product is thawed and developed right into a continuous account.While plastic extrusion is a generally used technique in production, the products made use of in this process significantly influence its final output. At its core, plastic extrusion includes changing raw plastic product into a continual profiled form. It has actually led to the growth of innovative extrusion machinery, which has actually boosted the efficiency and quality of the plastic extrusion procedure.In final thought, plastic extrusion is an intricate process that makes use of innovative modern technology and differed materials to create diverse items.
Report this page